Partnering to Prevent Exposure to Silica, Dust and Noise in Construction and Demolition (Completed – 2009-2014)
Susan Woskie, PhD
University of Massachusetts, Lowell
Ph: 978-934-3295
[email protected]
Jackhammers and pavement breakers, concrete saws and backhoes: the work of the equipment operators and the laborers who build bridges, pave roads, and knock down old buildings is synonymous with dust and noise. When workers aren’t protected from these hazards, respiratory disorders and hearing loss are just a matter of time.
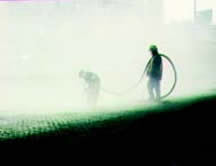
The silica dust hazard is clear in this photo of workers scarifying concrete. The hazard that can’t been seen is the noise level.
Drs. Susan Woskie and Anila Bello, and their research team at the University of Massachusetts at Lowell (UMass Lowell) worked with concrete and demolition contractors, workers, and the Laborers’ and Operating Engineers’ unions to explore the effectiveness and viability of a variety of controls to keep these dangers in check.
Researchers captured the attention of contractors and hygienists alike with a series of tests showing that outfitting concrete saws with water attachments could reduce dangerous airborne silica levels by 85%. But that’s not the only way wetter is better to control dust. In collaboration with a major demolition contractor, UMass Lowell researchers investigated the impact of simply spraying water from hoses and water cannons during demolition. Results indicated that this water suppression reduced workers’ exposure to silica and other dusts well below the OSHA PEL. The researchers then partnered with a manufacturer of one brand of water cannon, the Dust Boss, to conduct field experiments to estimate the amount of dust and silica reduction achieved from the use of this water suppression method.
The team completed testing of an “air curtain,” a dust control specially designed for use on bridge and overpass jobs. Application of the air curtain significantly reduced dust exposures in workers’ breathing zones, although it didn’t eliminate the need for respirators during chipping. Its feasibility in the workplace would depend on some modifications, a maintenance program, and worker training in its proper use.
In collaboration with the Operating Engineers’ Training Center, researchers evaluated noise exposures generated by many types of heavy construction equipment. Results indicated that for most equipment, the safe (85dbA) noise perimeter was 2-3 feet, but some equipment generated noise levels calling for workers to keep 16 to 42 feet away in the absence of hearing protection. The team evaluated how to apply the noise perimeter zone and engineering controls to reduce worker exposure and hearing loss.
- In partnership with two demolition contractors, one large crushing operation contractor and the Dust BossTM manufacturer/supplier, researchers evaluated the efficacy of different water suppression methods on reducing silica and dust exposures in construction demolition and crushing sites.
- In collaboration with the Operating Engineers’ Training Center in Canton Massachusetts, researches installed noise-reducing mats inside the two loudest heavy equipment machines used at this center.
- Researchers performed a qualitative evaluation of acceptance of active noise reduction (ANR) headsets at the Operating Engineers’ Training Center.
- The manuscript titled “Characterization of occupational and environmental exposures to crystalline silica and dust at demolition and crushing sites” is under preparation for submission to the Journal of Occupational and Environmental Hygiene.
- Researchers produced two reports with focus on demolition and crushing exposures to support OSHA documentation during public hearings for the proposed rule on occupational exposure to crystalline silica.